Understanding the Causes and Solutions for Undercut Welding in Metal Manufacture Procedures
In the realm of metal manufacture procedures, the event of undercut welding poses a considerable obstacle that demands an extensive understanding of its reasons and practical services. The elaborate interplay of different variables throughout welding operations can cause this unwanted phenomenon, affecting the architectural honesty and total high quality of the welded joints - Preventing weld undercut. By studying the root causes of undercut welding and discovering efficient restorative actions, fabricators can elevate the criterion of their handiwork and guarantee the production of perfect metal elements
Common Root Causes Of Undercut Welding
Frequently ignored in steel fabrication, undercut welding takes place because of various aspects that demand careful attention and expertise to be efficiently reduced. One typical source of undercut welding is excessive warmth input. When the warm input is too expensive, it can bring about the melting and subsequent disintegration of the base product along the sides of the weld joint, developing a groove or undercut. Furthermore, improper welding methods, such as using the wrong welding angle or take a trip rate, can likewise contribute to undercut development. Poor securing gas protection is an additional essential variable that can cause undercutting. Inadequate gas insurance coverage fails to protect the weld pool effectively, leading to oxidation and undercut problems. Furthermore, the option of welding parameters, such as voltage, current, and cable feed speed, plays a significant function in the event of undercut welding. Understanding these common causes is important for executing precautionary actions and ensuring top notch welds in metal fabrication procedures.
Effect of Incorrect Welding Parameters
Inaccurate welding specifications can significantly jeopardize the integrity and quality of bonded joints in metal manufacture processes. The impact of inaccurate welding specifications materializes in numerous means, resulting in architectural weak points and flaws in the bonded parts. One crucial aspect influenced by inappropriate welding parameters is the penetration deepness of the weld. Not enough heat input due to reduced welding currents or exceedingly high traveling speeds can lead to insufficient blend in between the base metals, leading to incomplete joint penetration and compromised bonds. Conversely, extreme warmth input brought on by high welding currents or slow-moving traveling rates can lead to burn-through and excessive reinforcement, producing a fragile and unstable weld framework. In addition, inaccurate parameters such as improper voltage settings or inaccurate electrode angles can add to irregular weld grain profiles, absence of fusion, and enhanced opportunities of problems like damaging. Thorough attention to welding specifications is extremely important to ensure the production of top quality welds with the desired mechanical homes and structural honesty.
Impact of Improper Lantern Angle
Incorrect torch angle in welding operations can considerably affect the high quality and honesty of the last weld joints in metal construction processes. The lantern angle plays an essential duty in determining the warmth input and distribution throughout welding. When the torch angle is inaccurate, issues such as undercutting can emerge. Damaging is a typical welding problem where a groove develops along the weld toe, weakening the joint and jeopardizing its architectural honesty.
A lantern angle that is as well steep can bring about inadequate infiltration, insufficient fusion, and enhanced spatter. On the various other hand, a torch angle that is also shallow can cause extreme infiltration, burn-through, and distortion of the base product. Preventing weld undercut. Appropriate lantern angle is crucial for guaranteeing regular weld quality, strength, and appearance
To stop damaging and various other problems caused by inappropriate lantern angles, welders should be educated to maintain the appropriate lantern angle throughout the welding procedure. Regular surveillance and change of lantern angles during welding can assist achieve sound welds with minimal problems.
Role of Inadequate Welding Methods
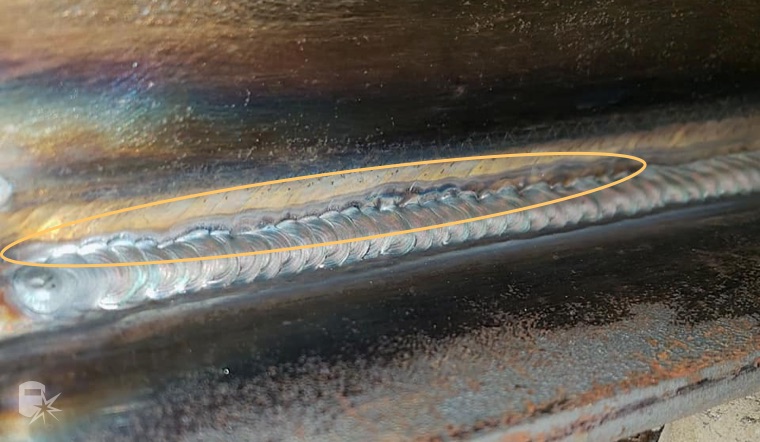
An additional facet of inadequate welding techniques is improper weld preparation. Inadequate cleansing of the base metals, incorrect joint design, or inadequate side preparation can all add to damage welding. Poor shielding gas coverage or utilizing the incorrect type of gas can result in insufficient combination and the formation of undercut flaws.
To resolve the duty of inadequate welding strategies in steel fabrication procedures, it is necessary to offer comprehensive training for welders. Proper education on welding criteria, joint preparation, and securing gas choice can aid avoid undercut welding and ensure top notch welds in steel fabrication tasks.
Effective Solutions for Undercut Welding
Attending to undercut welding in metal fabrication needs executing effective remedies to boost weld quality and architectural integrity. Among the main services to battle undercut is to change welding parameters such as voltage, current, and travel rate to guarantee appropriate warm input and fusion. By fine-tuning these setups, welders can stop excessive melting of the base metal and filler product, minimizing the probability of undercut learn the facts here now development.
In addition, correct joint preparation is essential in stopping undercut. Guaranteeing clean base steel surface areas complimentary of contaminants and utilizing the proper bevel angle can assist promote far better weld infiltration and reduce the risk of undercut - Preventing weld undercut. Utilizing suitable welding strategies, such as oscillating the lantern or weaving, can likewise aid in dispersing warm equally and filling up the weld joint sufficiently, lessening the opportunity of undercut flaws
Furthermore, choosing the right welding consumables, consisting additional hints of electrodes and filler metals, is important in alleviating undercut. Using materials with suitable chemical structures and mechanical properties can add to accomplishing audio welds with marginal undercut. Routine assessment and quality assurance measures must additionally be carried out to detect and attend to undercut issues promptly, making certain the general integrity of fabricated metal parts.

Conclusion
In conclusion, understanding the causes and solutions for undercut welding in metal manufacture processes is vital for accomplishing premium welds. By resolving common reasons such as inaccurate welding specifications, improper lantern angle, and poor welding methods, welders can stop undercutting and make certain solid, resilient welds. It is important to focus on these factors and implement efficient services to boost the general welding procedure and final item quality.
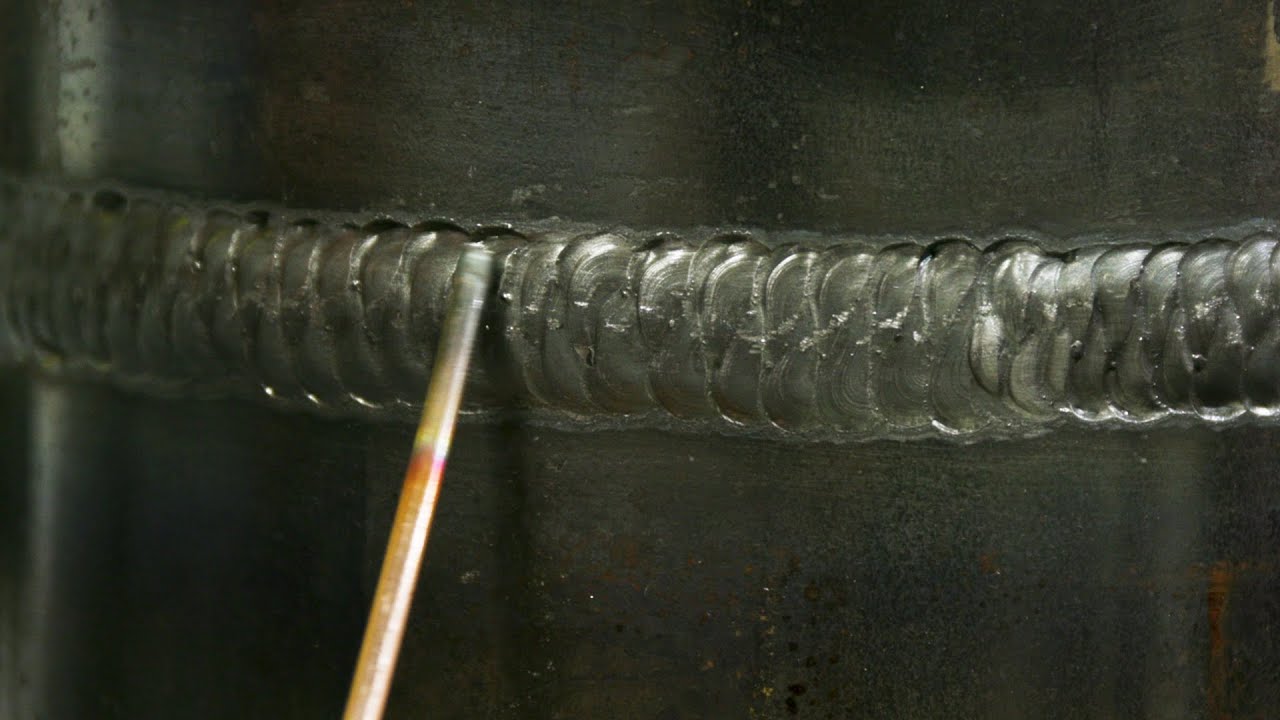